ENTEX temperature control units utilise high-quality materials, fittings and instruments to ensure the best-possible system availability.
It goes without saying that ENTEX complies with the applicable standards and guidelines, including DIN 4754 (for organic heat transfer media / thermal oil), DIN 4752 (for water), the EMC Directive 2014/30/EU, the Machinery Directive 2006/42/EC, the Pressure Equipment Directive (PED) 2014/68/EU and the AD 2000 Regulations.Pressurised-water units are generally used for temperatures up to 220 °C. Oil units are used for higher temperatures (up to 430 °C). The modular series are produced with power ratings of 6–350 kW (electrically heated) and throughputs of 3–350 m³/h. However, more powerful systems are also possible on request.
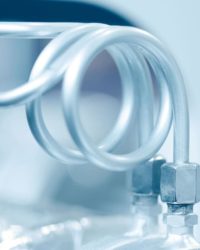
Extruder tempering
Precise and efficient temperature control
The importance of heating and cooling technology cannot be overestimated – and not just for extrusion processes. It is a key determinant of product quality, and plays a major role in resource conservation and economic efficiency.
ENTEX has developed its own temperature control units to ensure that its Planetary Roller Extruders enjoy top of the line tempering. In fact, these units are now also being used outside the field of extrusion technology.
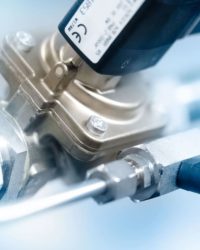
Thermodynamics
Application areas
- Plastics industry
- Rubber industry
- Chemicals
- Pharmaceuticals
- Composites
- Electronics
- Wood processing
- Paper industry
- Mechanical engineering (OEM)
Typical uses
- Extruders
- Rollers
- Presses
- Tanks
- Tools
- Mixers
Temperature-Control-Units (TCUs) from ENTEX
TEMPERING SYSTEMS – TYPE DYNAMIC
Technical data and equipment
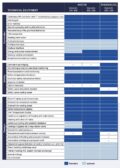
Saving energy efficiently
Rising energy costs are a fact of life, and it is for both ecological and economic reasons that ENTEX offers alternatives to the electric heating that has been standard to date in temperature control units.
Conventionally fired units in which the necessary energy is supplied by natural gas, light heating oil or special fuels are possible alternatives.
In this case, ENTEX uses mixing circuits that rely on these primary energy sources. These can be equipped with a highly efficient direct feed if the identical medium is being used, or with a heat exchanger that keeps different media separate from one another. In both cases, it is no longer necessary to make use of significantly more cost-intensive secondary energy in the form of electricity.
As a result, energy is used more effectively and energy costs are lower. That is not only good for the environment – it also saves money.
Our scope of products and services includes an individual project study that helps the customers to decide in advance which solution would be best for them.
PROJECT STUDY
Experience with various heating and cooling technologies
Gas-heated systems and electrically heated systems: a comparison
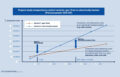
Impressive tempering solutions
Thanks to our high level of vertical integration and our custom engineering, we are able to build tempering solutions that are perfectly suited to the application at hand, taking into account both the customer’s needs and the conditions on site.